E’ ben noto come il metallo prezioso per eccellenza, a seconda dei suoi impieghi, venga legato con altri metalli come l’argento a formare, ad esempio, la tipica lega impiegata in gioielleria al titolo di 750 millesimi o, in modo equivalente, a 18 carati.
Per quanto riguarda invece l’oro da investimento, questo è definito come tale dalla normativa italiana solo se avente una purezza pari o superiore a 900 millesimi per quanto riguarda le monete oppure pari o superiore a 995 millesimi per quanto attiene ai lingotti. Questi ultimi, in molti casi, vengono prodotti con finezza di almeno 999 millesimi, se non - addirittura - fino a 999,9999 millesimi.
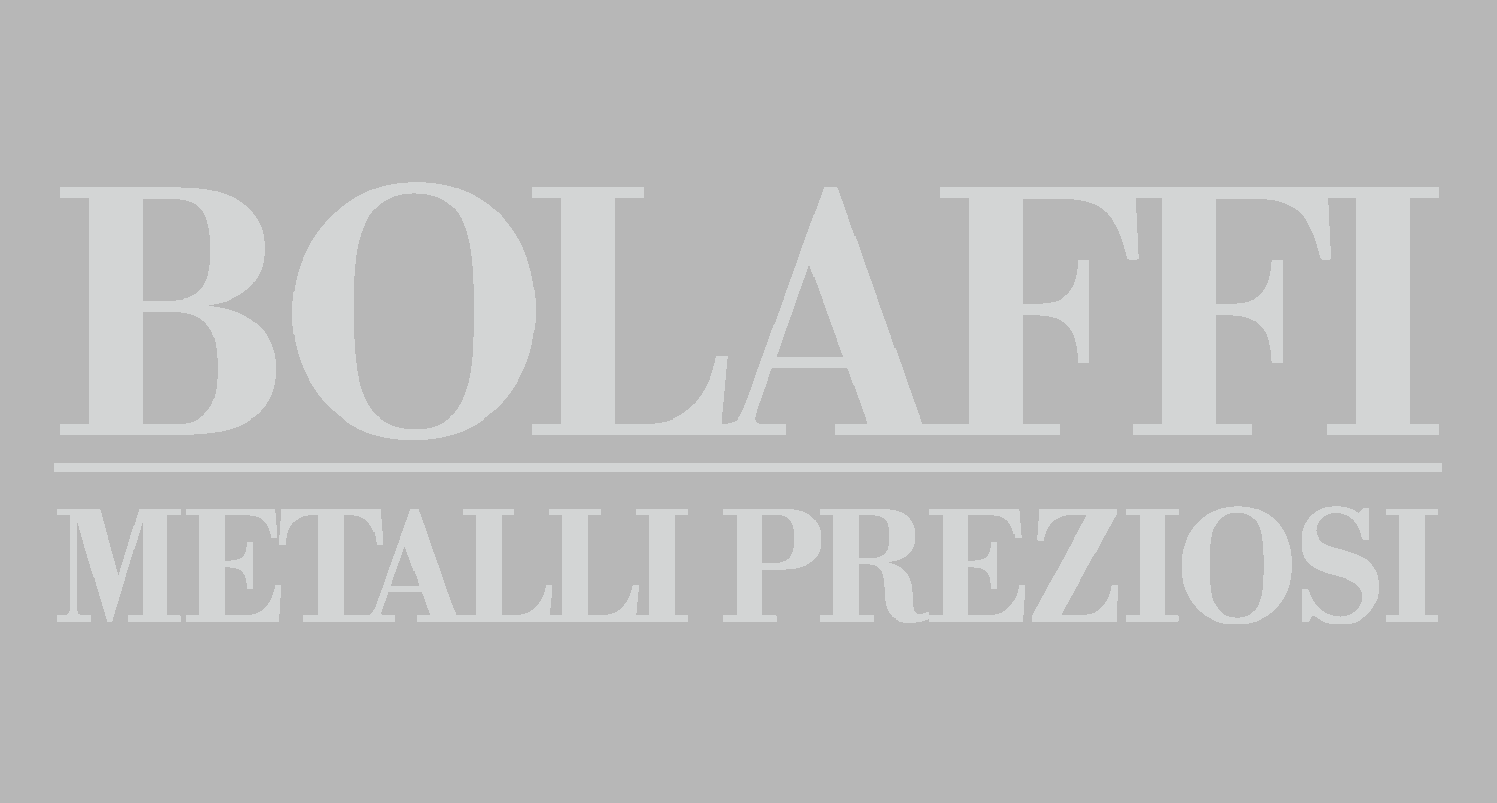
Ma quali sono le tecnologie attualmente impiegate per la raffinazione del metallo prezioso? La raffinazione dell'oro con acqua regia è uno dei processi di affinazione chimica dei metalli preziosi più utilizzati e collaudati, e viene effettuato in impianti industriali dotati di attrezzature realizzate ad hoc, che garantiscano risultati del tutto soddisfacenti.
L'oro può anche essere portato alla purezza voluta mediante raffinazione elettrolitica dell'oro, ma il metodo maggiormente utilizzato è proprio quello che prevede l'utilizzo della cosiddetta acqua regia, un mix di acido cloridrico e acido nitrico in proporzioni ben definite che fa sciogliere il metallo prezioso come se fosse un cloruro. La soluzione ottenuta viene quindi sottoposta a diversi processi chimici, fino ad ottenere dei frammenti di oro privo di impurità, che a quel punto può essere fuso e trasformato in graniglia, lastre o lingotti.
Gli impianti per l'affinazione dell'oro con acqua regia sono di due tipi: uno è il classico impianto di affinazione oro di tipo “statico”, che consente di mettere in pratica tutti i processi, dall'analisi preliminare della lega alla vera e propria affinazione dei metalli, fino alla fusione dell'oro finale, mentre l’altro è il cosiddetto impianto “a buratto” caratterizzato dalla presenza di un cilindro rotante a velocità regolabile, la cui rotazione fa sì che la graniglia di minerale aurifero ancora impuro si possa sciogliere completamente, inoltre può lavorare in completa autonomia, senza la presenza fisica di un operatore.
La raffinazione elettrolitica dell’oro è invece un processo molto più antico, messo a punto nel 1863 e che comporta la dissoluzione elettrolitica di un anodo d’oro impuro in un elettrolita contenente acido cloridrico con successiva deposizione, sul catodo, del metallo prezioso che così possa raggiungere una purezza del 99,99%.
L’argento, il platino e altri metalli presenti nell’oro impuro si separano come fanghi e vengono recuperati, mentre i metalli non preziosi restano in soluzione. Questo metodo è ampiamente usato nella raffinazione del cosiddetto “oro primario”, quello estratto dal minerale, ma di solito non è impiegato per la raffinazione su piccola scala per ragioni di costi elevati, dovuti all’immobilizzo dell’oro utilizzato nell’elettrolita e negli elettrodi.
La raffinazione del metallo prezioso costituisce dunque un procedimento industriale costoso e complesso e che coinvolge dispositivi ad elevata tecnologia e competenze professionali di alto livello. Per questo, “si fa presto a dire ‘oro puro’…”.